Beyond Visibility: Why Live Data from the IoT Holds the Key to Cold Chain Excellence
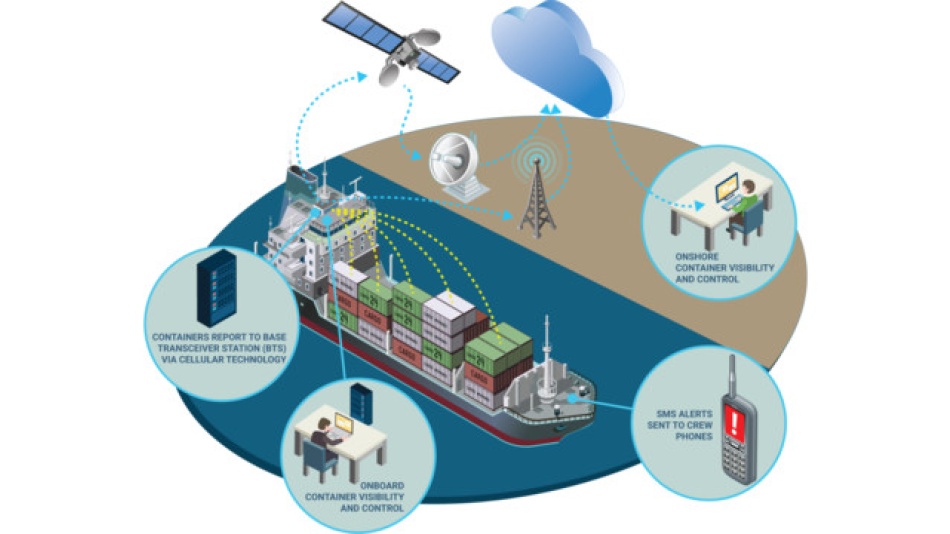
(Source: http://www.foodlogistics.com, Sue Rutherford). We are entering an exciting phase in the deployment of Internet of Things (IoT) technology and solutions in supply chain management and operations. Worldwide, we are witnessing an explosion of smart, connected things, exploiting technological advances and reduced costs in telematics devices, sensors, applications, software and communications networks. Analyst IHS Markit predicts that the IoT market will grow from 15.4 billion devices in 2015 to 30.7 billion devices in 2020 and 75.4 billion in 2025.
By incorporating IoT technologies and solutions into supply chain networks, we can seamlessly connect business processes, such as shipping and receiving, with people, data and things, such as pallets, containers, trailers, warehouses, distribution centers (DC), terminals and yards, to run these networks at maximum efficiency.
The coming IoT generation will be driven by products and solutions that are much more software centric, with robust cloud technology and an open architecture that enables connectivity of fixed and mobile telematics devices, sensors and actuators. This next generation technology will provide for “multi-tenancy,” or the ability to easily encompass different ecosystem participants, such as shippers, third-party logistics providers (3PL), carriers, ports, DCs and hauliers, in a single IoT network—and the flexibility to work with different IoT devices and technologies.
With these kinds of platforms in place, and the choice of technologies multiplying rapidly, IoT can become integral to supply chain communities, helping beneficial cargo owners (BCO) and their logistics and transport providers to safeguard shipments, manage timelines, proactively mitigate delays and breakdowns, comply with regulations, increase operational efficiency across the network, break down silos, and launch new data-driven business services.
As supply chains become more complex and regulated, managers everywhere need to know what is going on across their entire network, communicating with suppliers, customers and, often, government agencies at the same time. Any weak points in the chain can cause problems—and where temperature-sensitive food is involved, these problems can escalate all too quickly.
Getting a Handle on Hand-offs
Supply chains, especially cold chains, are particularly vulnerable at hand-off points, where different lines of business meet, or where a supplier’s process meets a customer’s process. In a typical international refrigerated container shipment, such hand-offs typically occur at the ship-port interface, during transfer of containers to/from port by truck, rail or inland waterway, and when devanning goods from containers for cross-docking or storage prior to onward delivery by truck—or vice versa from origin to outbound port.
Processes at these hand-off points are still often manual. What data exists generally lives in silos and often is “after the fact.” As a result, hand-offs frequently lack visibility and control, resulting in errors that can have serious negative downstream effects.
Take a typical cold chain process, when chilled or frozen goods are unloaded from a deep-sea reefer container into a cold store and then onto a reefer truck for landside delivery. Despite having good temperature control, the reefer’s door could be open for too long, affecting the quality of the product loaded closer to the door. Or the case of a reefer container arriving at a seaport or other supply chain node and not being put on power. Or pallets of fresh produce being loaded too hot into a reefer box or trailer in the first place, ultimately resulting in shortened shelf list, reduced revenue and possible cargo loss. Then there are the perennial challenges of equipment malfunction and human error, leading to cold chain deviations and breakdowns.
Making the Invisible Visible
Improved IoT technology makes locating, monitoring and addressing these errors far simpler. What was previously invisible becomes visible, allowing informed, data-driven decisions to be made, versus a historic “blame and claim” culture that is ultimately very costly for all involved and does nothing to actively tackle what the Food and Agriculture Organization of the United Nations estimates as more than a 30 percent worldwide wastage of food from farm to fork at an annual cost of $890 billion.
Maersk Line, currently the largest adopter of IoT technology among reefer container carriers, says that in the first six months of 2017 alone, its Remote Container Management (RCM) system alerted the company “to more than 4,500 incorrect temperature settings on customers’ reefers.” It added that in 200 of those cases, “the setting inaccuracy was severe enough that had RCM not notified Maersk Line personnel [who] then made the necessary changes, the cargo—collectively worth several million dollars to our customers—would have been lost.”
IoT also can help break down information silos, making it easier to comply with regulations, such as the Food Safety Modernization Act (FSMA), which require visibility and traceability throughout the food supply chain. It also can help build a better relationship with customers at the end of the supply chain, for example, making it easier and quicker to recall product in the event of contamination or compromise, ship perishables out of the DC earlier than scheduled, or re-route to a closer destination to maximise shelf life.
Ultimately, it is supply chain execution that can really determine customer satisfaction and loyalty. Announcing recently that it will share IoT data with its clients—a long-awaited moment for BCOs who have been calling for visibility into the reefer “black box” for many years now—Maersk Line argued that “with more reliable data available, the customer can work more strategically on developing products and optimize processes along the entire supply chain. With full history of the conditions during transport, it also becomes possible to take agile decisions as to how products can be optimally treated after transportation.”
Of course, the food supply chain is already awash with data—commercial, legal, regulatory and operational. All this latent data potentially can deliver operational and business value when properly mined on a massive, automated scale, as various start-ups are now aiming to do. But all too often, the information on which today’s supply chains run is fragmented and unreliable—not surprising, given how much manual keying and rekeying still is involved and how many parties are involved along the complex journey from producer to end consumer.
Reliable, Real and Real-time Data
By contrast, data from IoT-connected containers, chassis, gensets, trucks and vessels is reliable, real and real-time. It reveals what is, versus what was planned or anticipated, shining a light not just on asset operations—crucial though they are—but on the fundamental supply chain processes, flows and hand-offs that make or break a shipment.
Announcing its investment in 350 new smart refrigerated containers earlier this year, U.S. carrier TOTE Maritime says that a core value is in “providing clients [with] crucial real-time, end-to-end visibility of their shipments in TOTE Maritime’s cold chain.” Expediting cargo distribution and providing the “precise monitoring and record-keeping” needed for FSMA compliance were also cited as key benefits.
Having deployed smart reefers since 2011, TOTE recently invested in new on-ship cellular GSM technology to provide on-board and shore-side monitoring of reefer shipments, closing the real-time traceability gap at sea. Maersk Line has similarly equipped its whole vessel fleet, and further such investments are anticipated in the future as vessels become generally more connected for diagnostics, schedule management, crew welfare and cargo care.
So, What Does the Future Hold?
Today, the big drivers for much IoT investment by cold chain asset owners revolve around better fleet utilization; reduced maintenance, repair (M&R) and claims costs; regulatory compliance; and security. However, a growing number of operators are starting to think about how they can deliver extra value beyond transporting or storing goods by helping their clients achieve new levels of shipment visibility, velocity and more proactive cold chain management. Indeed, end-to-end real-time visibility may in due course simply become an accepted cost of doing business.
But before we get ahead of ourselves, it’s worth remembering that we are in the early stages of the journey. Though an estimated 80 percent of the U.S. OTR reefer trailer fleet is now fitted with IoT telematics and sensors, only around 13 percent of the 2.7 million TEU global reefer container fleet is likewise equipped. Most container ships similarly are not GSM-enabled for wireless reefer box monitoring. Meantime, shippers and 3PLs focused on the shipment, rather than the means of transport, are not sitting idly by, deploying a growing range of cargo-level devices and sensors for live monitoring of in-transit condition and location.
As IoT technology continues to advance and industry practices evolve, we may expect to see more convergence of asset-level and cargo-level monitoring in the future. Indeed, some traditionally asset centric IoT providers in the cold chain space already are starting to add more cargo level and trip-based monitoring capabilities via acquisition or organic research and development. Current reality may not yet match up to the aspirations, but the technology genie is well and truly out of the bottle. Change is coming, and the current and next generation of IoT technology will be central to cold chain transformation—in ways we probably don’t yet even grasp.
Sue Rutherford has more than two decades of global marketing and business development expertise in the technology sector. As the vice president of marketing for ORBCOMM, Rutherford is responsible for advancing the strategic direction of ORBCOMM marketing and its leading M2M/IoT solutions.